The oiled wood was quite a mess and I finally decided that it wasn't such a good idea because it attracts dirt and mold.
On the handrail bases the dirt was way into the wood so I had to sand out all the black shit. Once sanded and all the oil removed I decided to cover them with Bristol Finish.
I had received a new gallon kit from the company because I complained about it, so I may as well use it ($150.00 per gallon). When I think back I had followed the CPES instructions to apply CPES and then when it is still tacky apply the Bristol Finish. This was a bad idea because CPES out gasses for days and may have lifted the Bristol Finish. So I decided to give it another try.
|
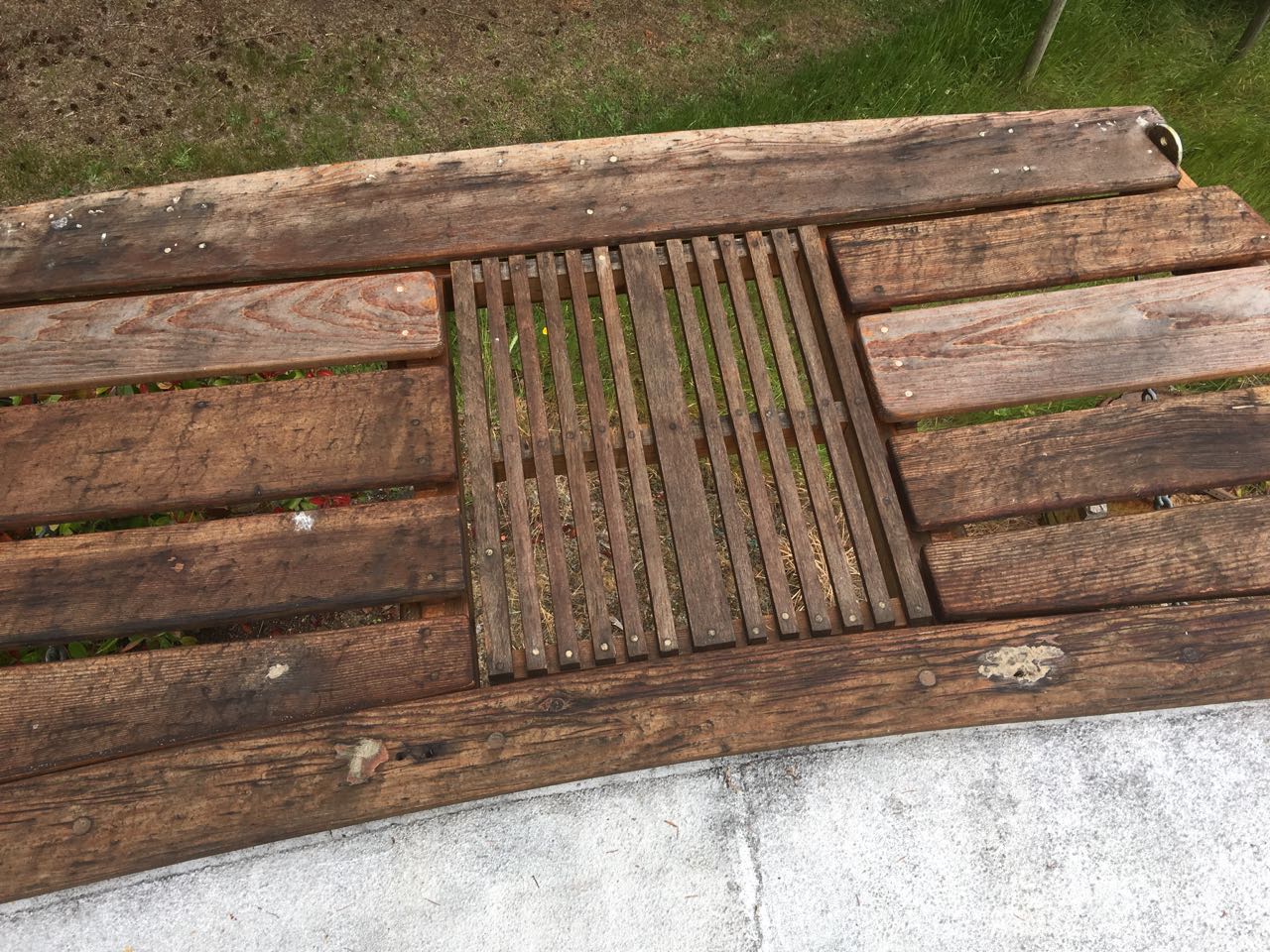 |
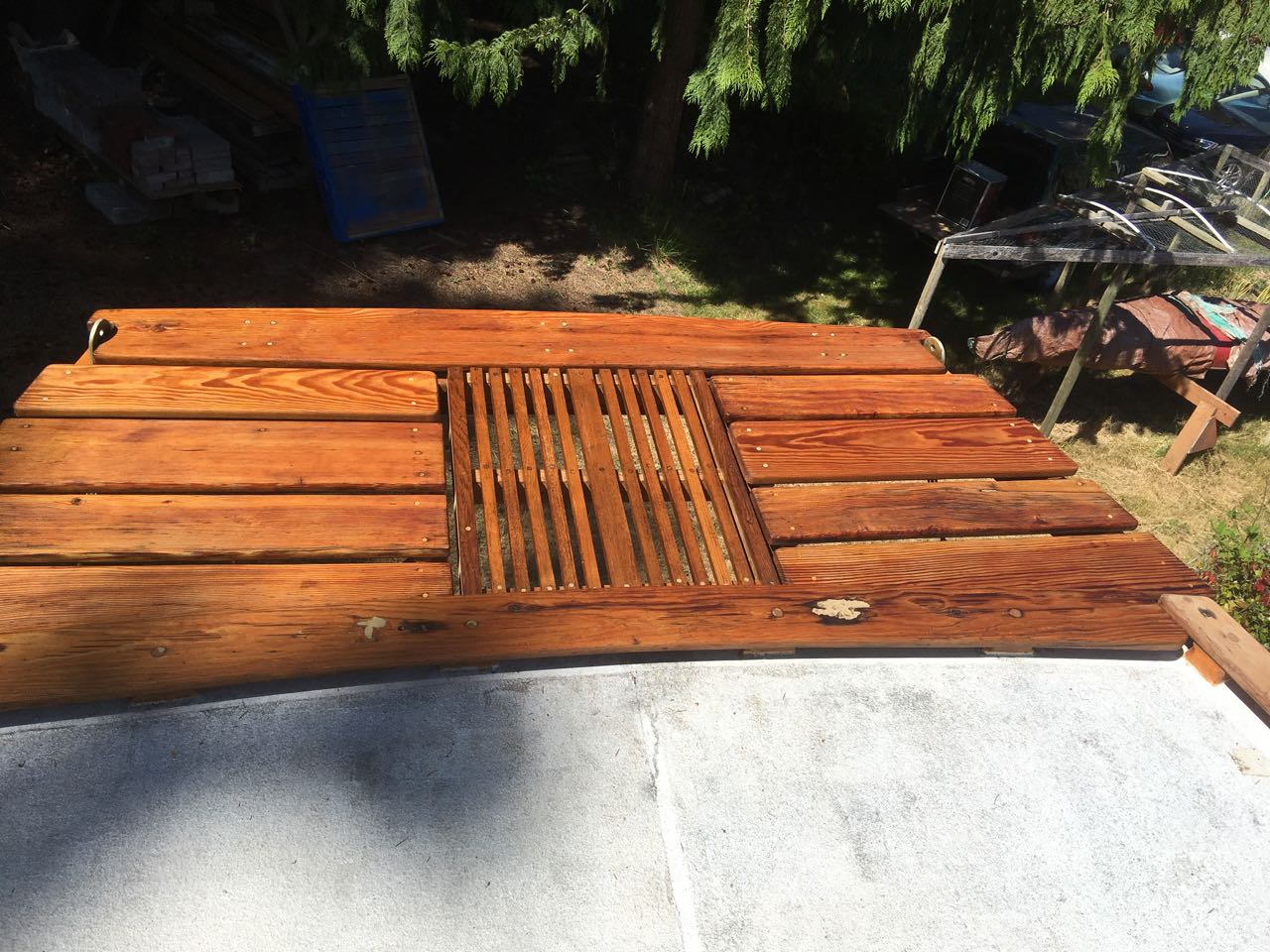 |
Boom kin... Before |
Boom kin after a little elbow grease. It will be protected for the winter but if the Bristol Finish holds out on the handrail bases I'll redo it in Bristol Finish. If not then we are back to Cetol.. |
|
|
The old wood hand rail spindles rotted at the bottom. New spindles range from about $30.00 to $50.00 each plus I not happy always dealing with wood rot. So I decided to go way out on the limb and use 2" PVC pipe schedule 40 instead of wood. Should be stronger or as strong as the wooden stanchions.
I will cut the bottom of a pvc pipe to fit the proper angles, then insert a threaded pin through a hole near the bottom and bolt it down to the hand rail base.
Then they will get painted black and covered with black rope. Should look pretty nice when they are done.
|
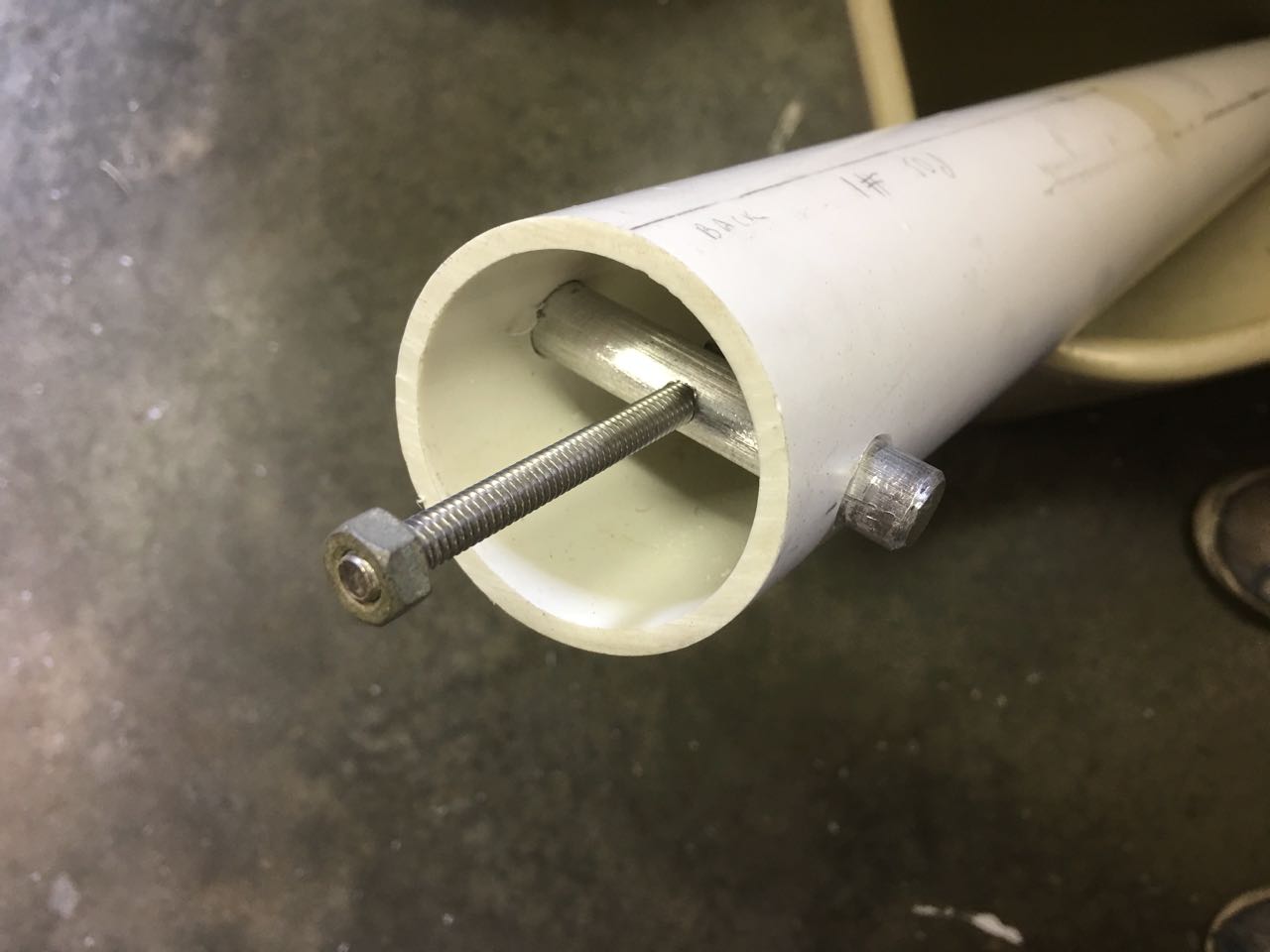 |
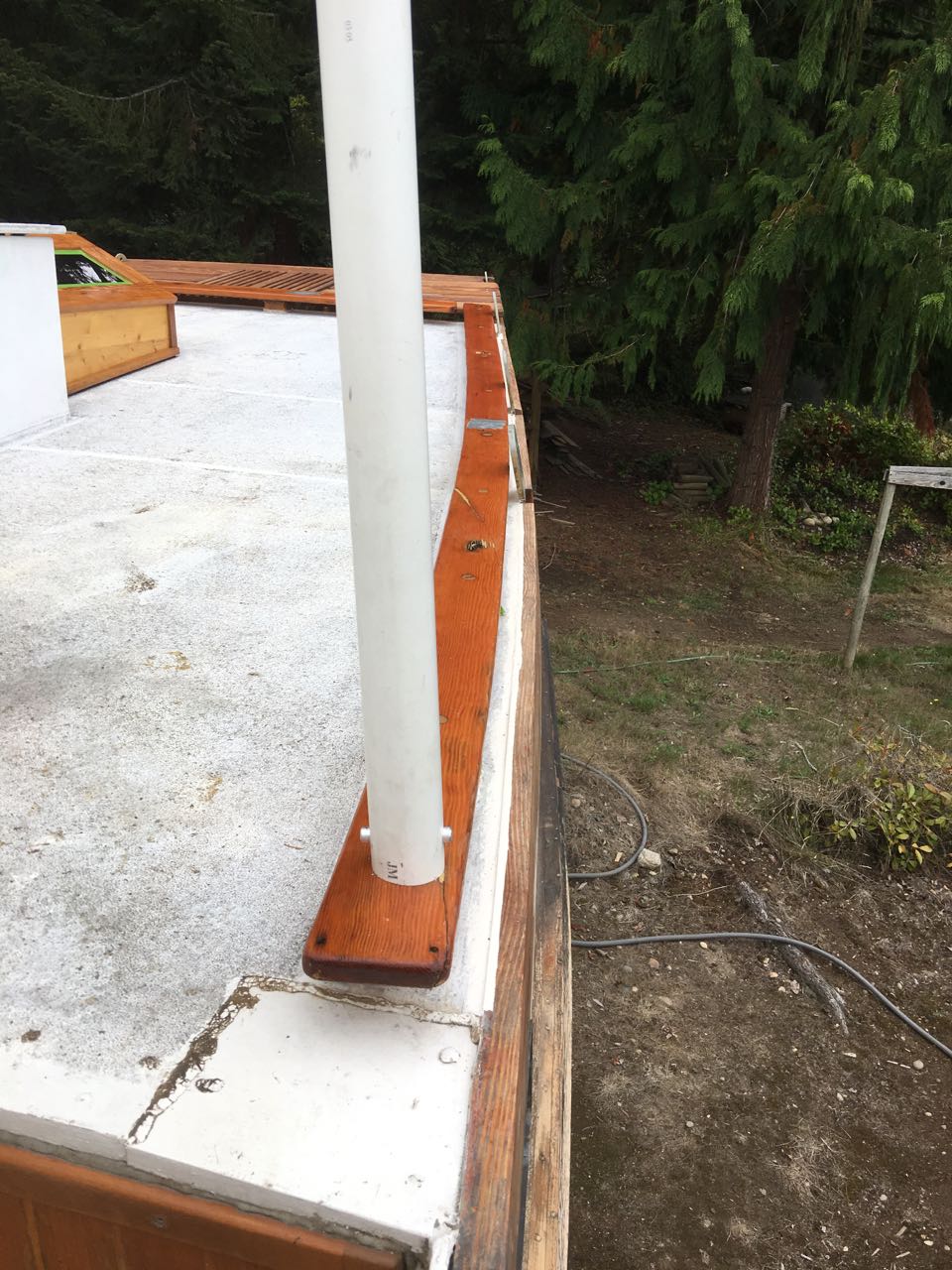 |
I made a bunch of pins that I threaded for 1/4" x 20 bolts. Then the pin is inserted through the pipe and the 3" bolt is fed through the top. Then a nut and lockwasher areused to snug the bolt to the pin. This prevents it from turning out when the nylon insert nut is used to hold it down to the handrail base. |
Here is the first one all figured out. The angle of the spindle has to match the angle of the hull coming up from the waterline when looking aft. When looking to the side it has to be vertical.
Minimum height requirements are 30" from deck to the top of the hand rail. When looking aft the top has to parallel to the bottom of the hand rail base. When looking at the side it has to be 90 degrees.
Will have to notch out the top of the pipe to fit the hand rail. |
|
|
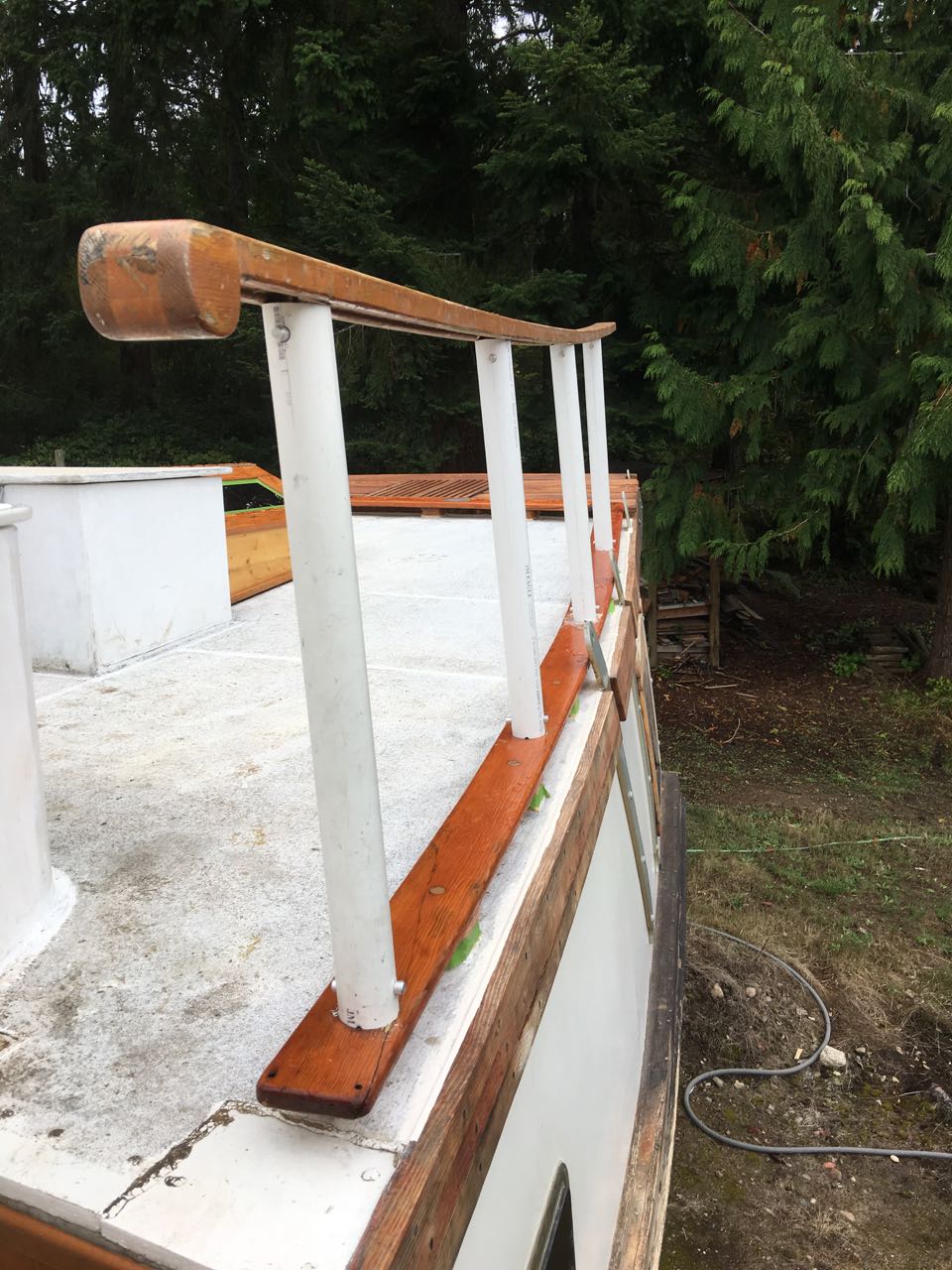 |
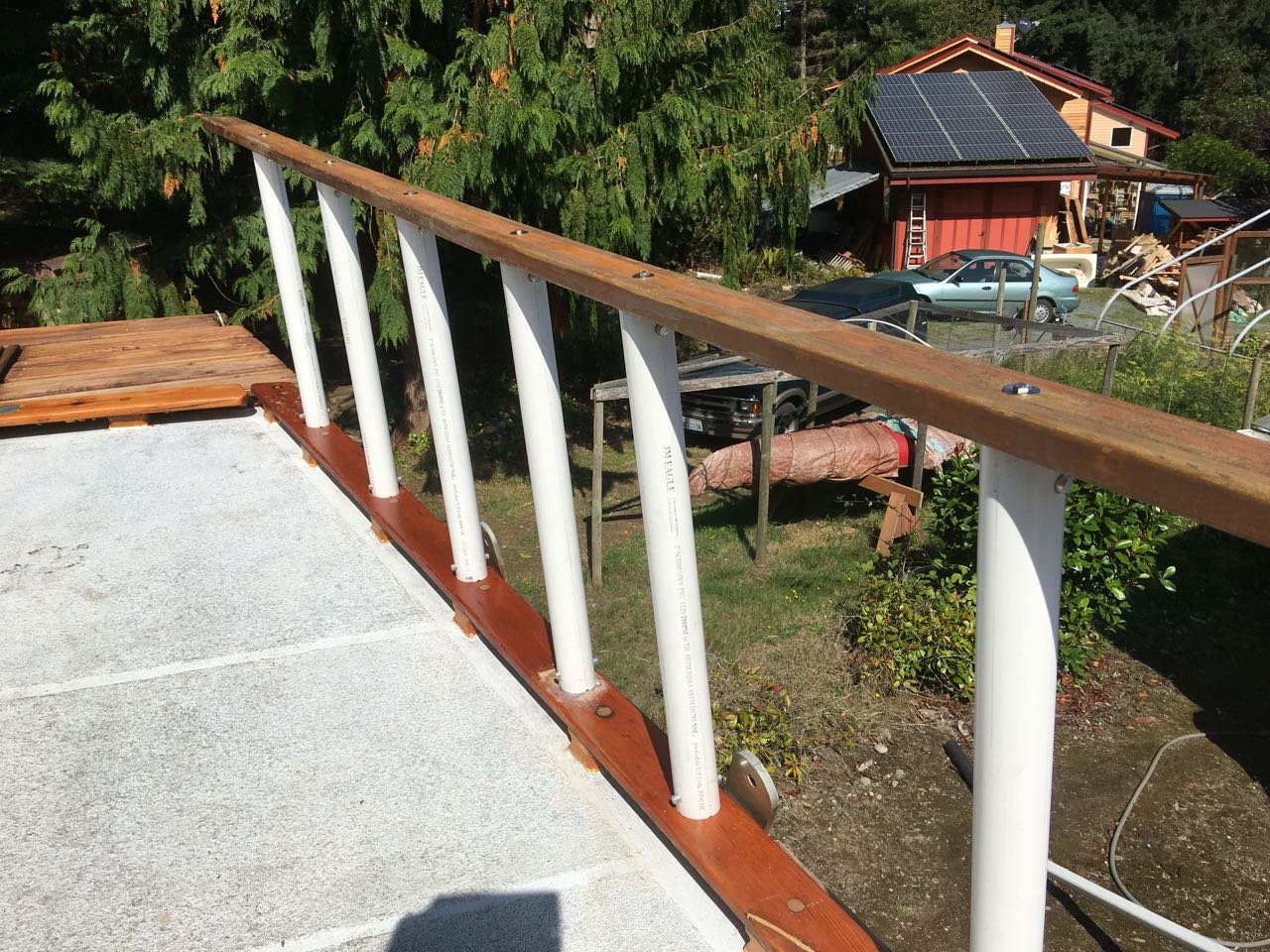 |
Got 4 of them in place then decided to see if the old hand rail will fit. YIKES! IT DOES !!
By the looks of it all I need to do is ream out the wood under the handrail instead of notching the stanchions. |
8 stanchions fitted into place. |
|
|
 |
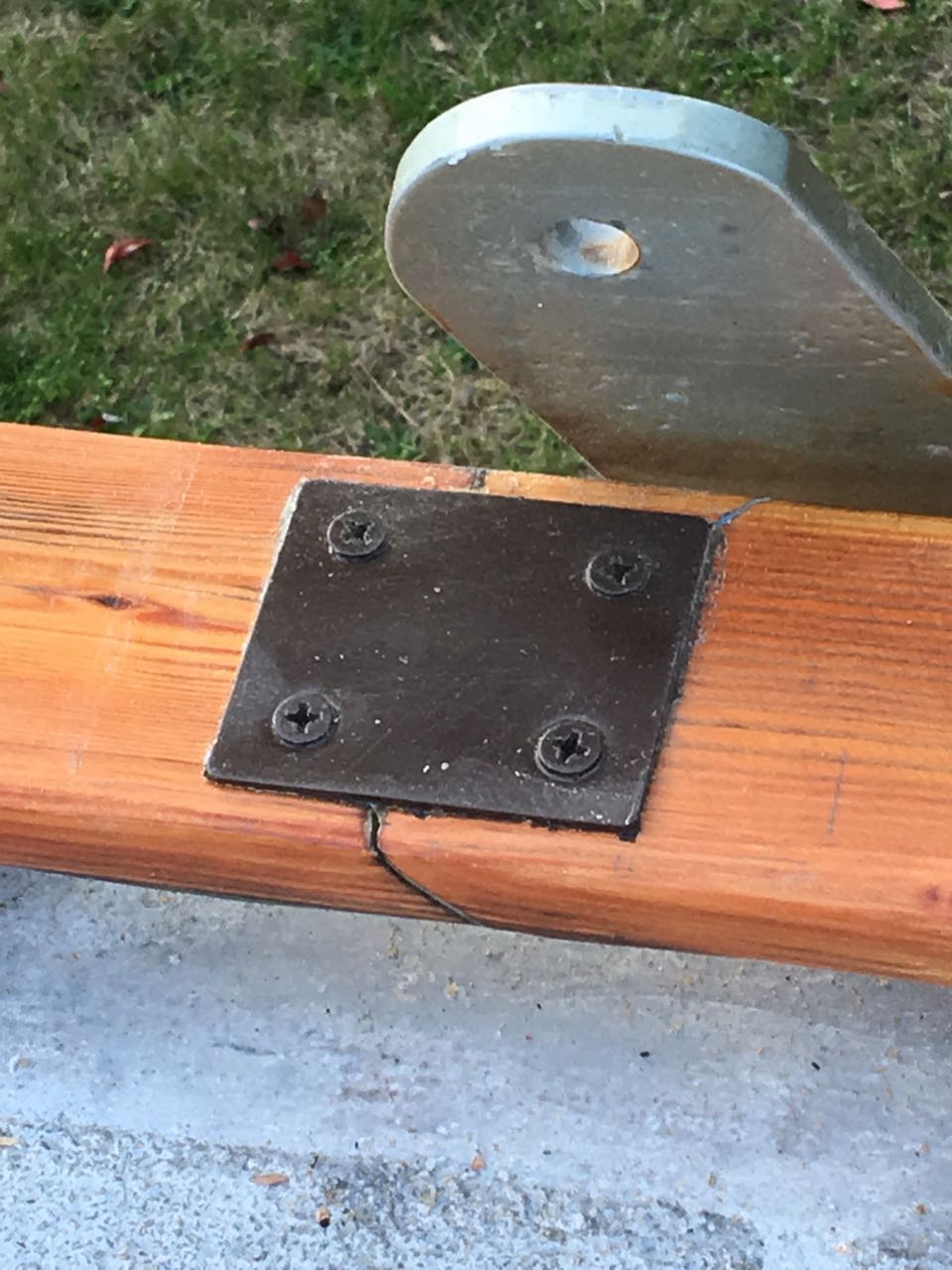 |
This damn splice has never stayed glued together. It even seperated using West System epoxy. Must be a lot of stress on the joint, or I should have made the scarf larger. Anyway, time now to clamp it for good. |
Aircaft aluminum plates top and bottom with glue squished in between and painted. |
|
|
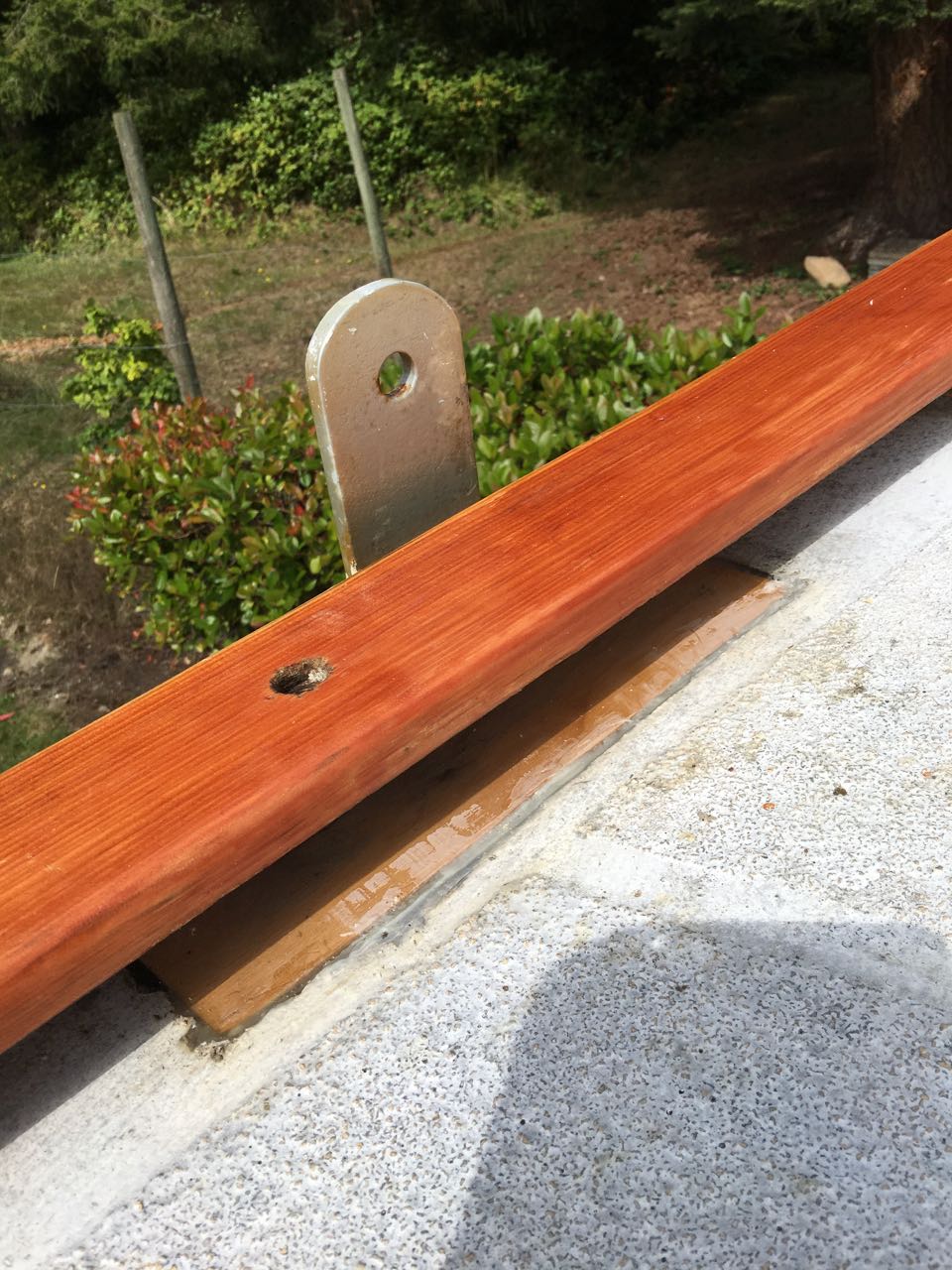 |
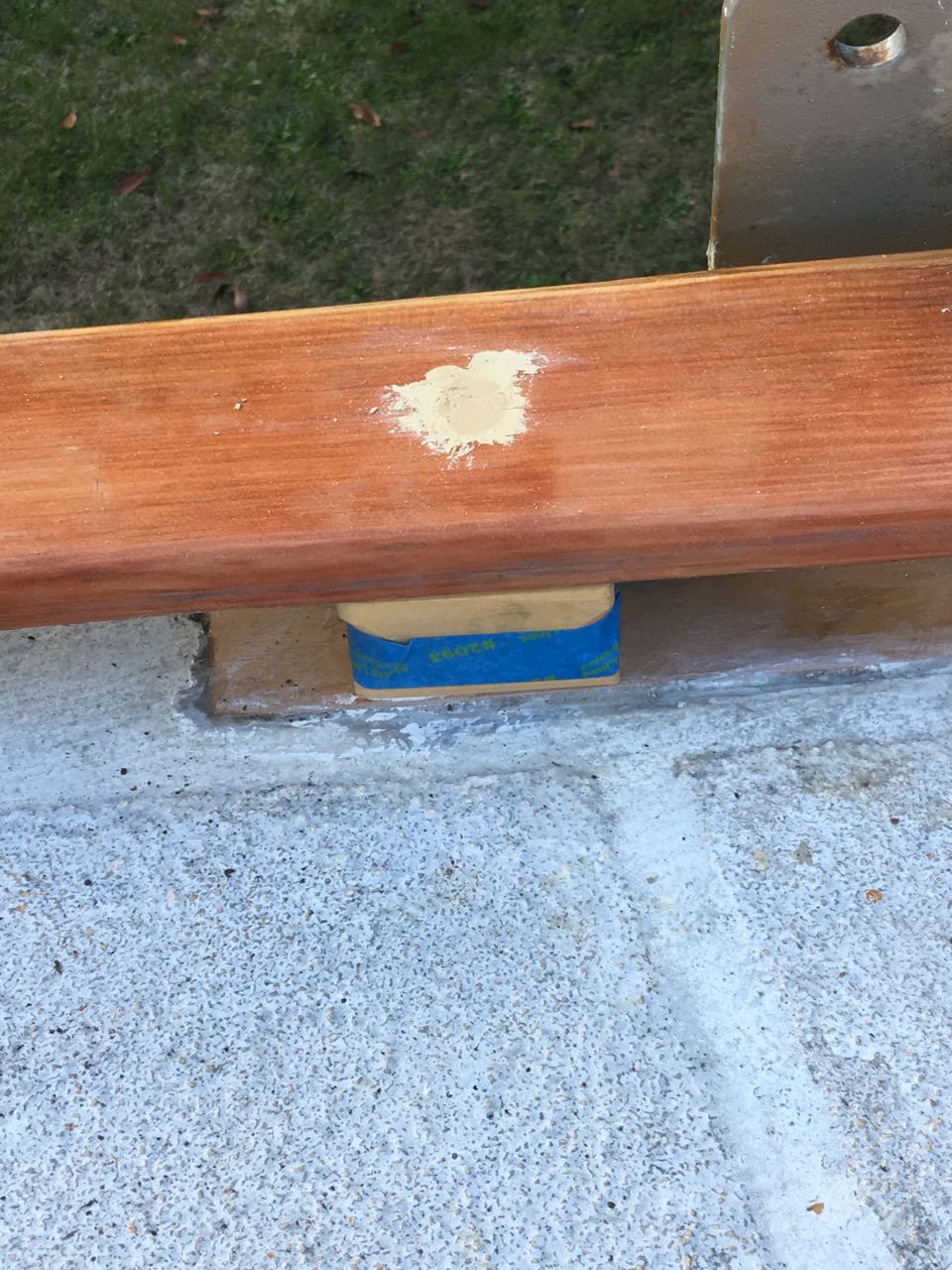 |
This is an area where I discovered some rot. In order to do the repair I had to remove a handrail base support block. |
Screwed and glued in the new block, and filled the bolt hole. Next is new rubber on the base. |
|
|
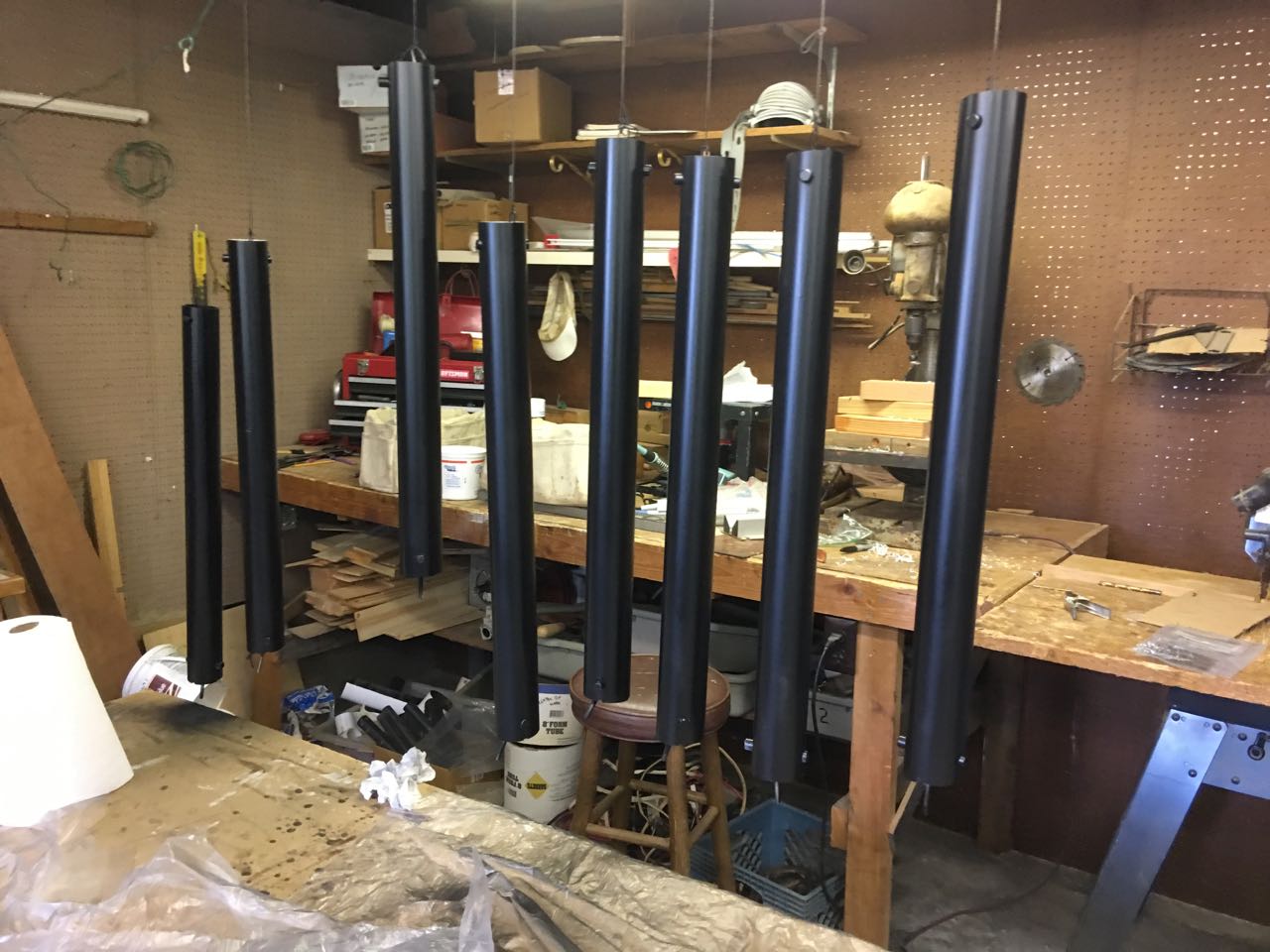 |
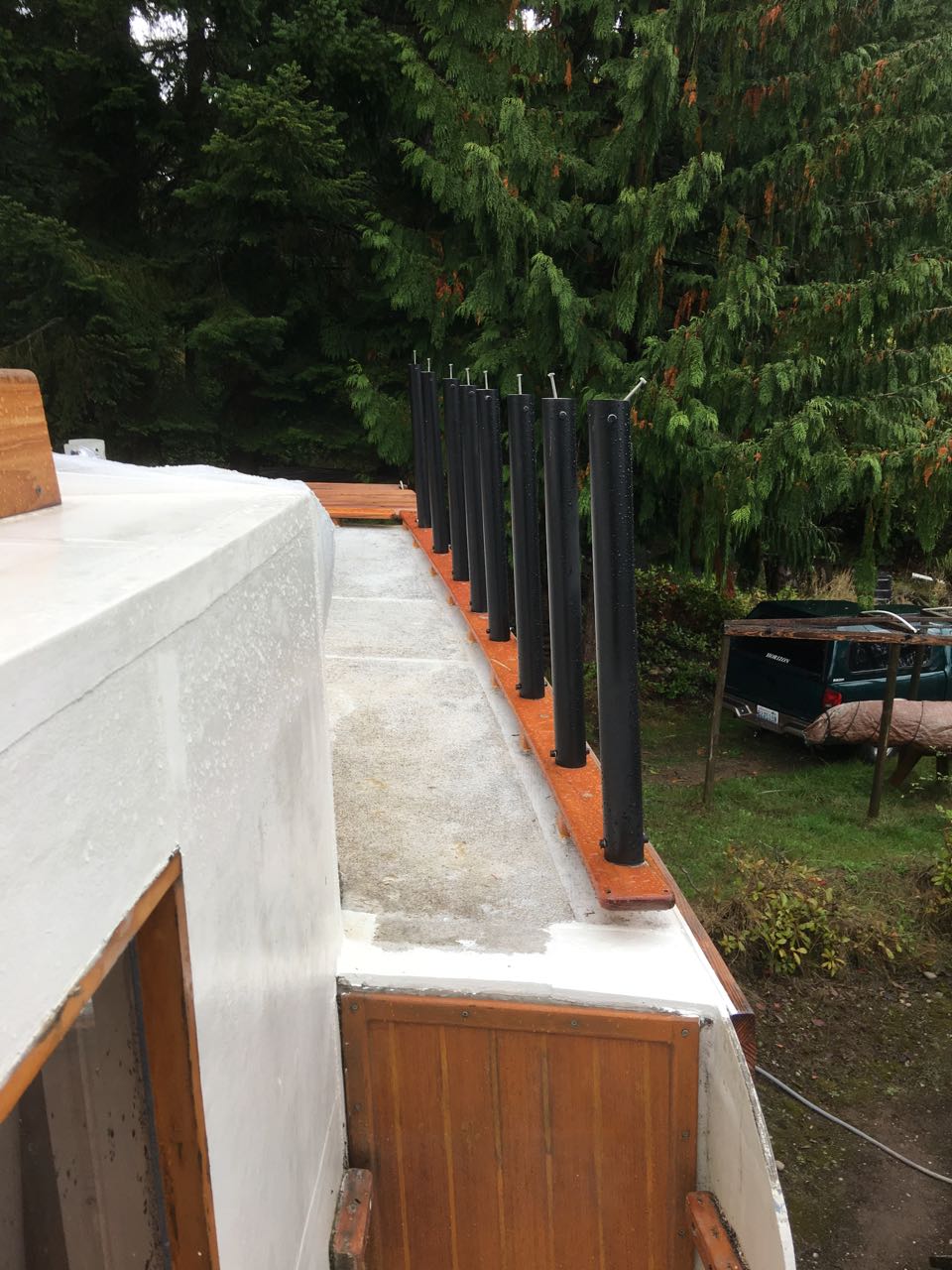 |
All painted black so the white will not show through the black rope work. |
Mounted on the base ready for the handrail. |
|
|
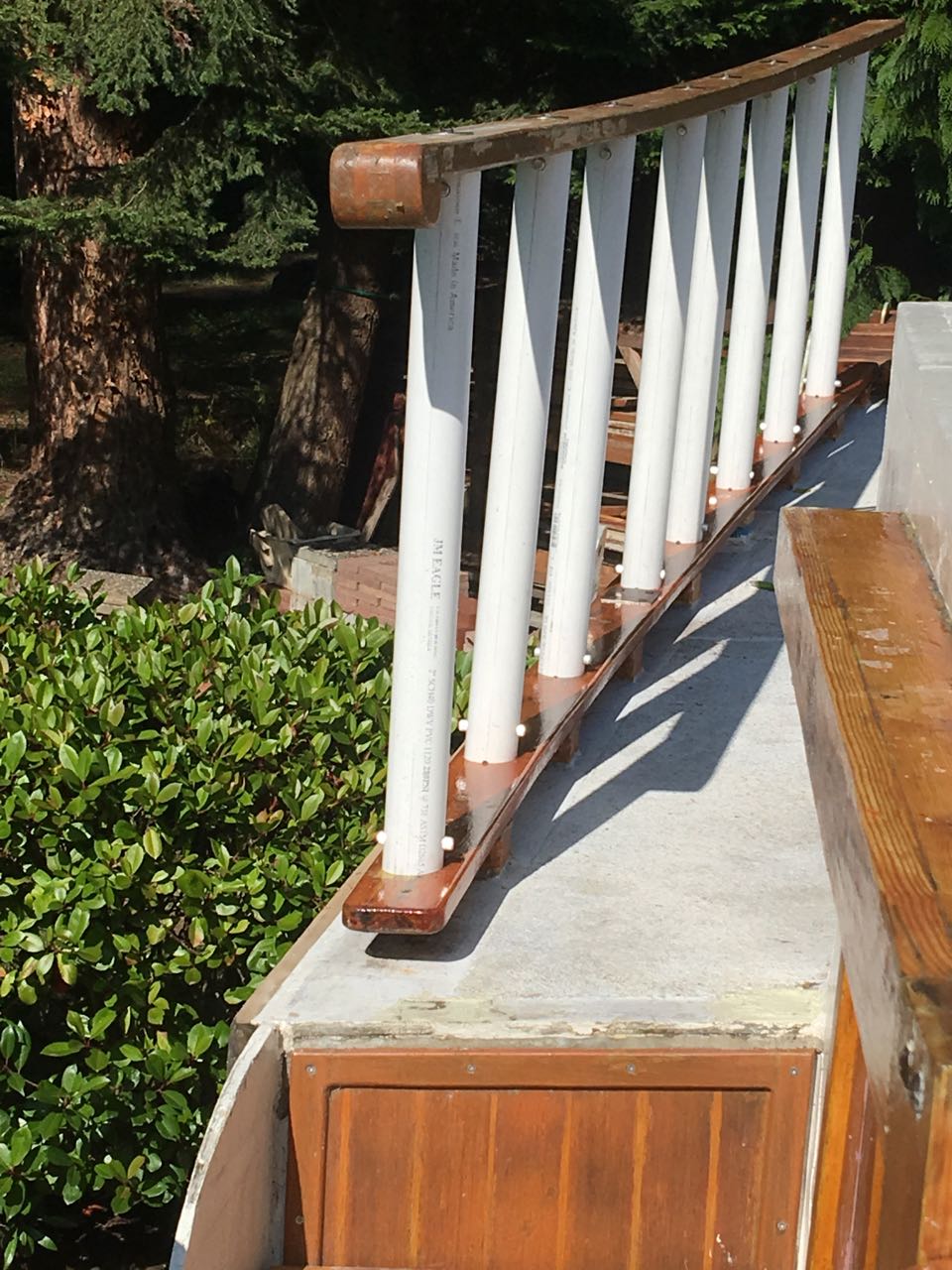 |
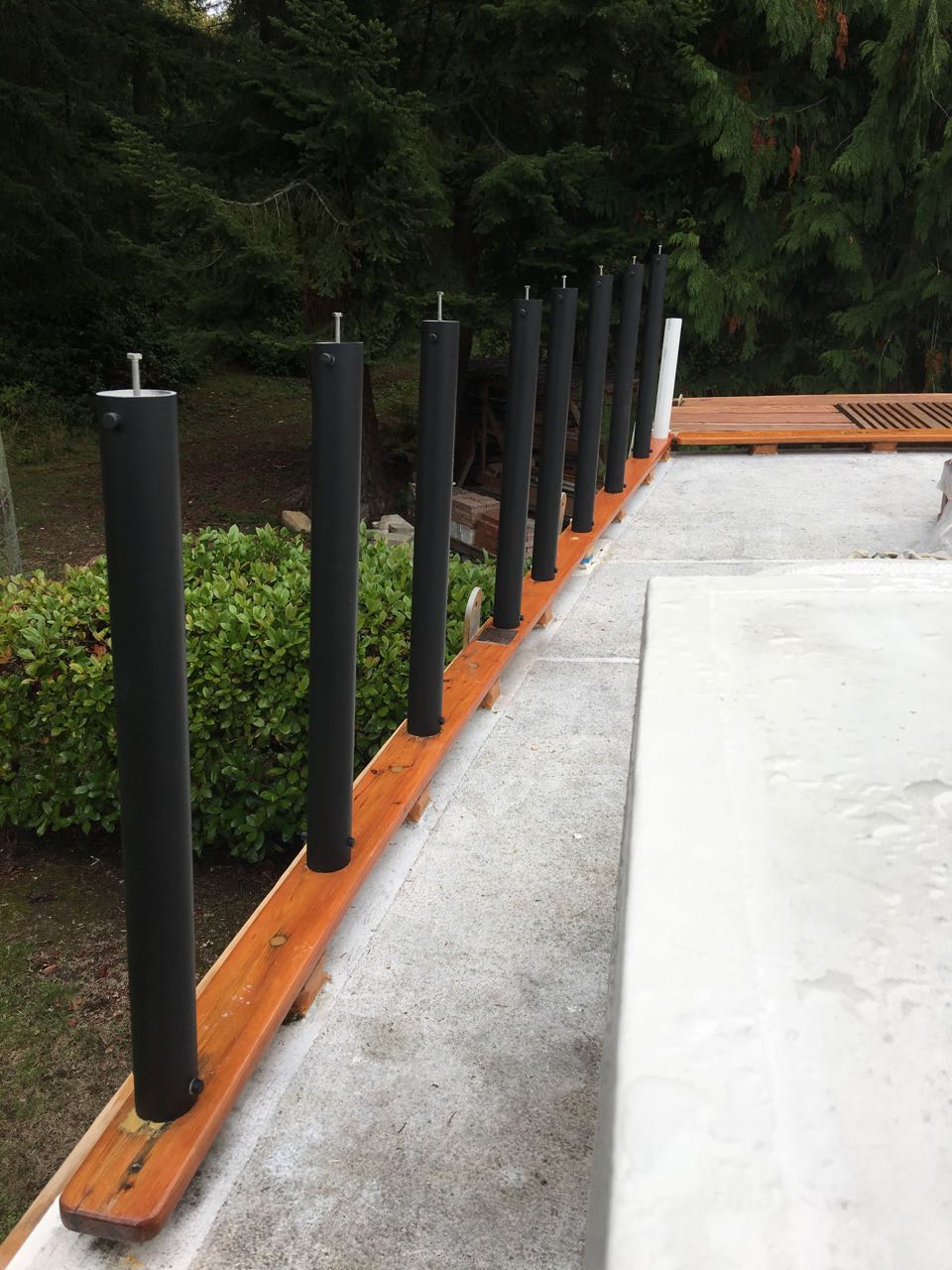 |
Starboard side stanchions and hand rail all put together. Handrail will need sanding and varnishing and stanchions painted black. |
Painted black and ready for handrail. |
|
|
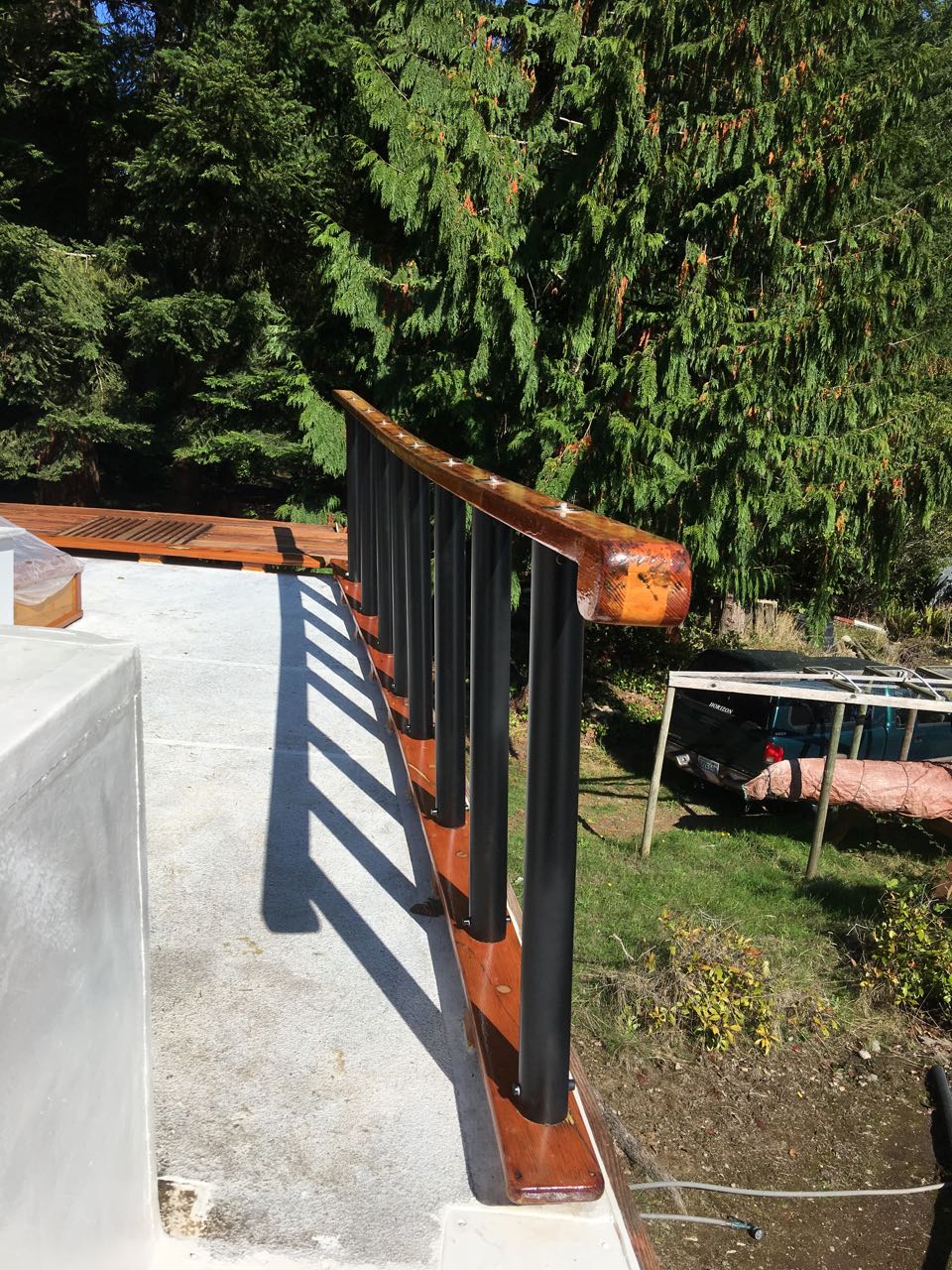 |
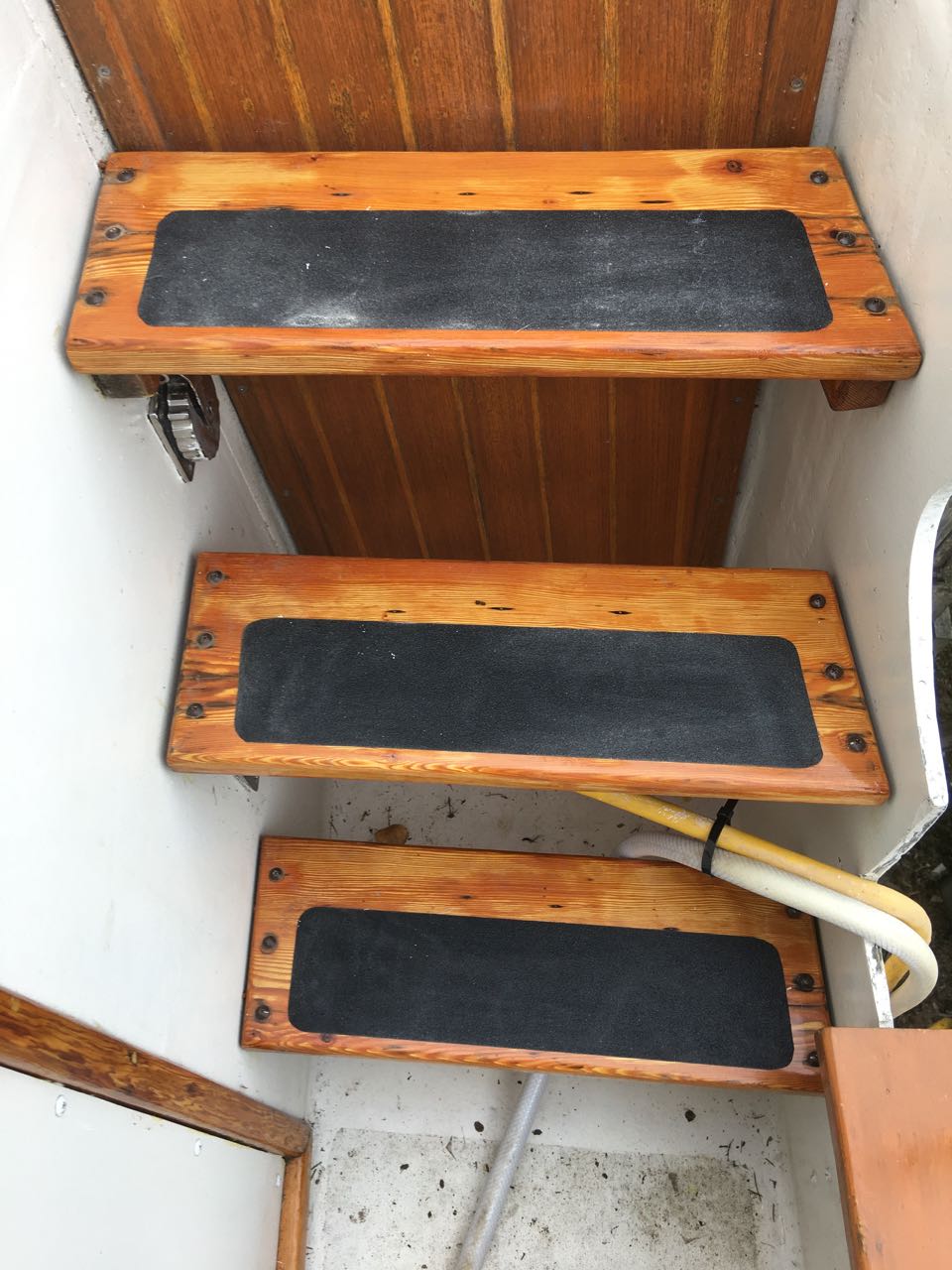 |
Port side done. |
Port stairs refinished and no-slip installed. |
|
|
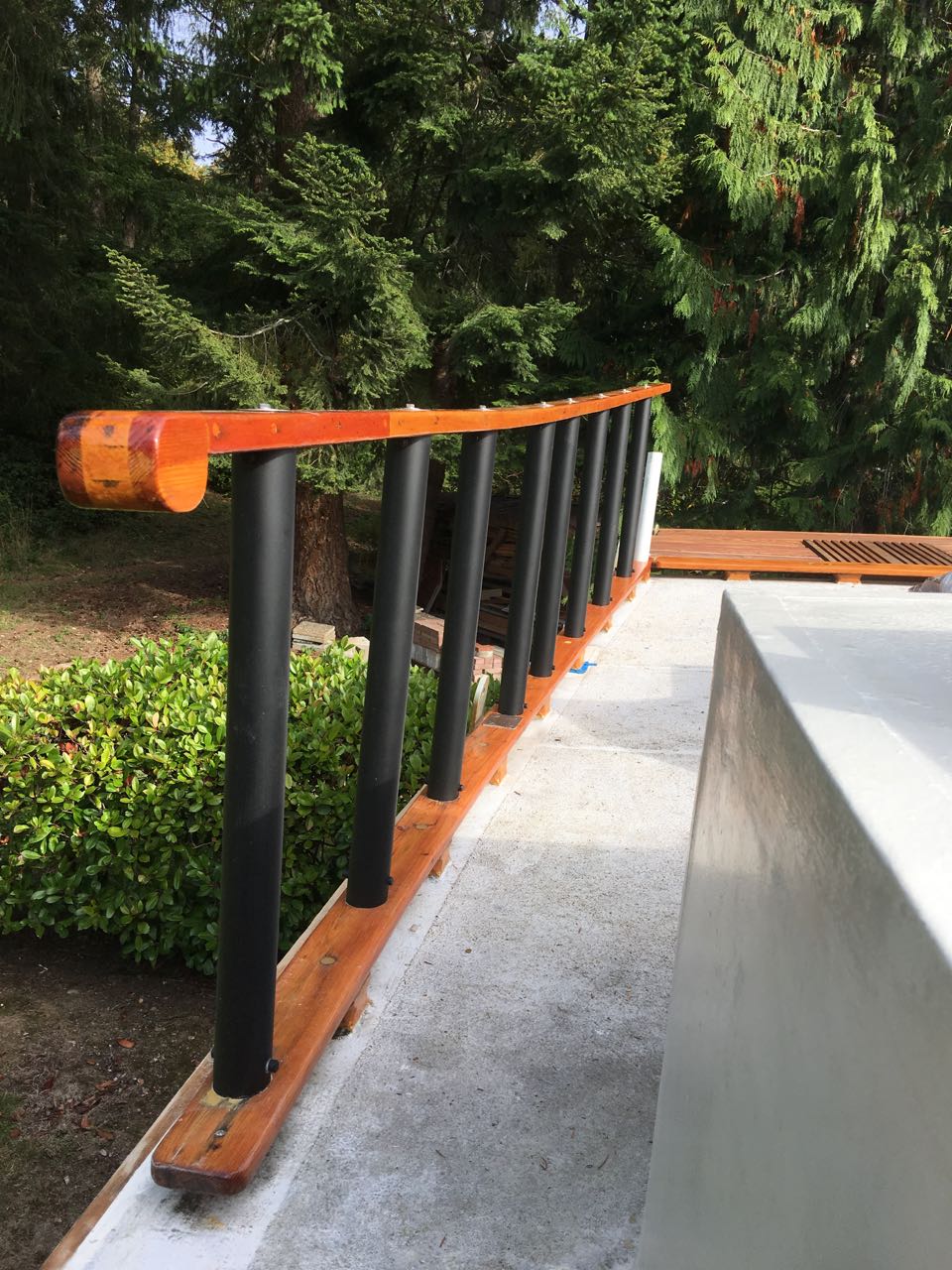 |
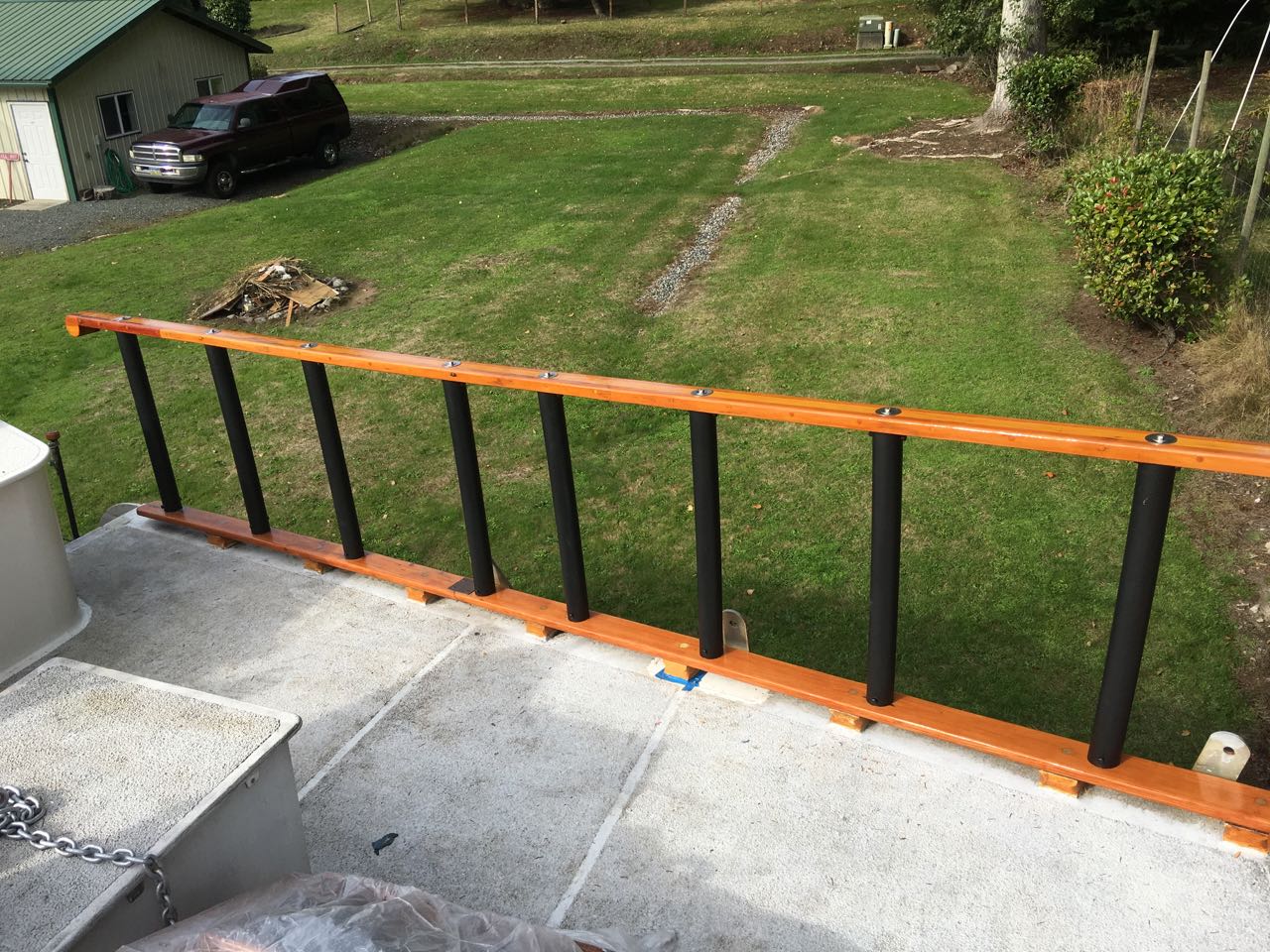 |
Starboard side handrail is on ! |
View from onboard. Feels safer up there now. Next is the aft handrail. |
|
|
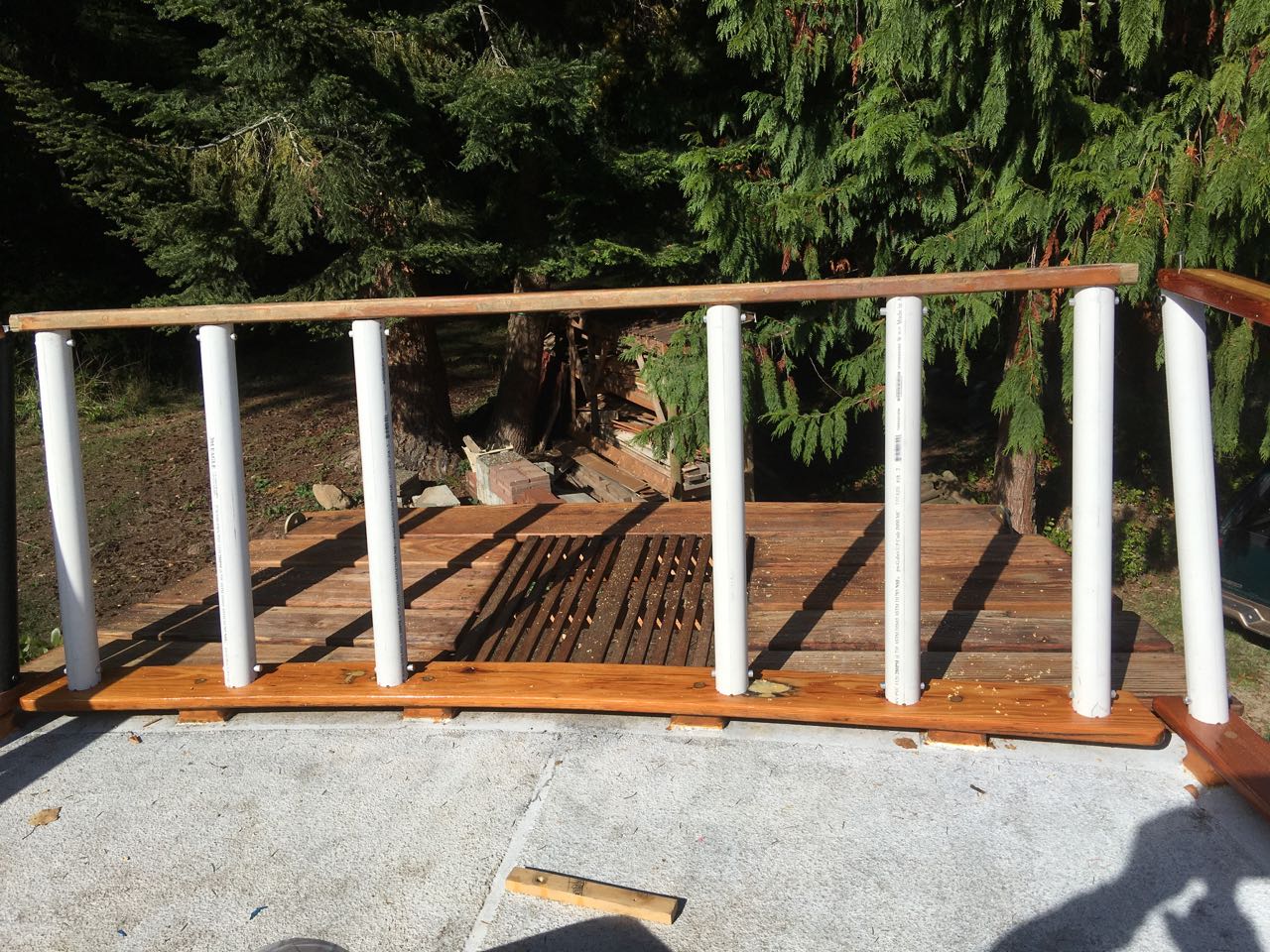 |
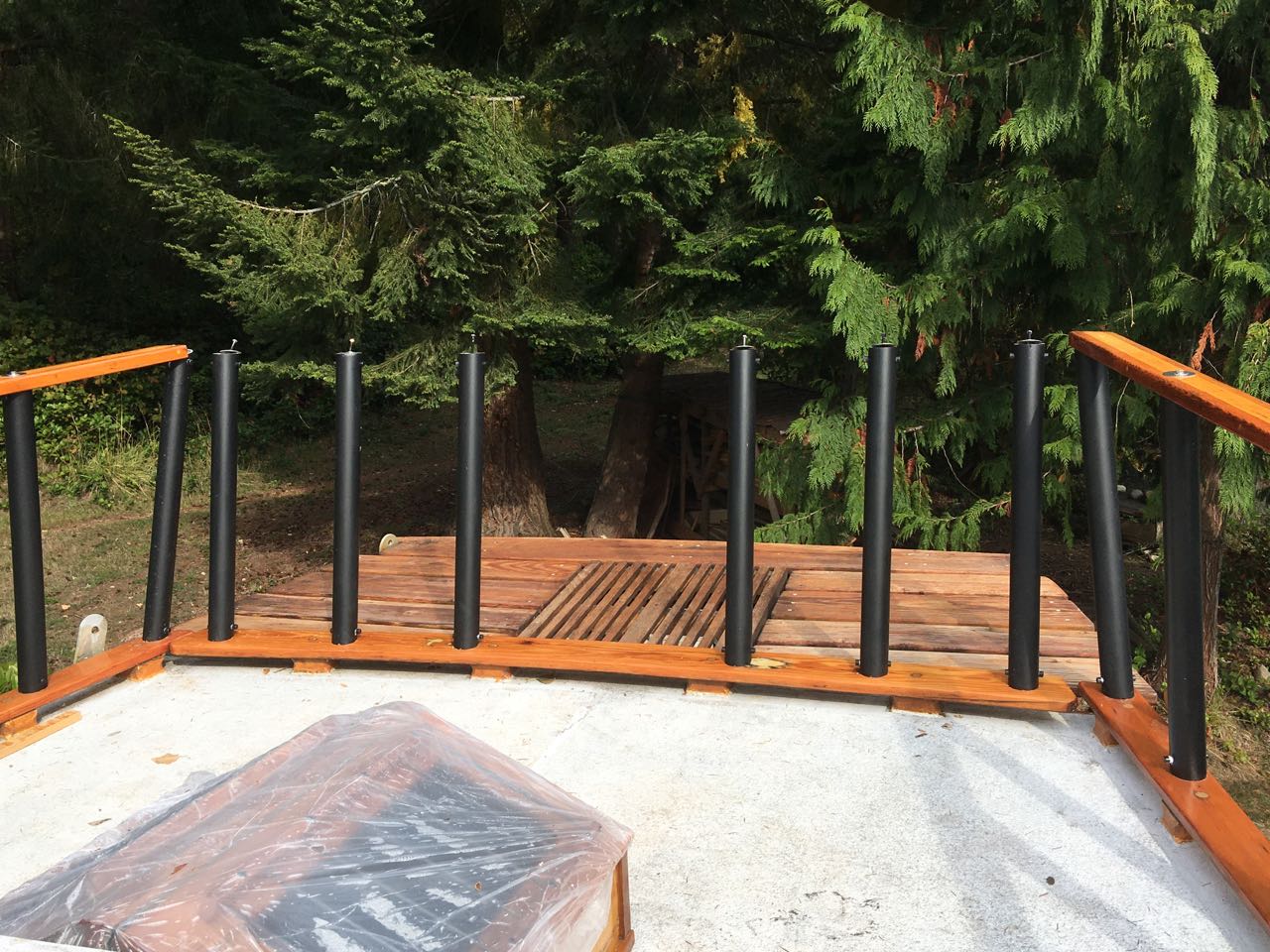 |
Aft handrail roughed in. What a job !! |
Painted black, ready for the handrail. |
|
|
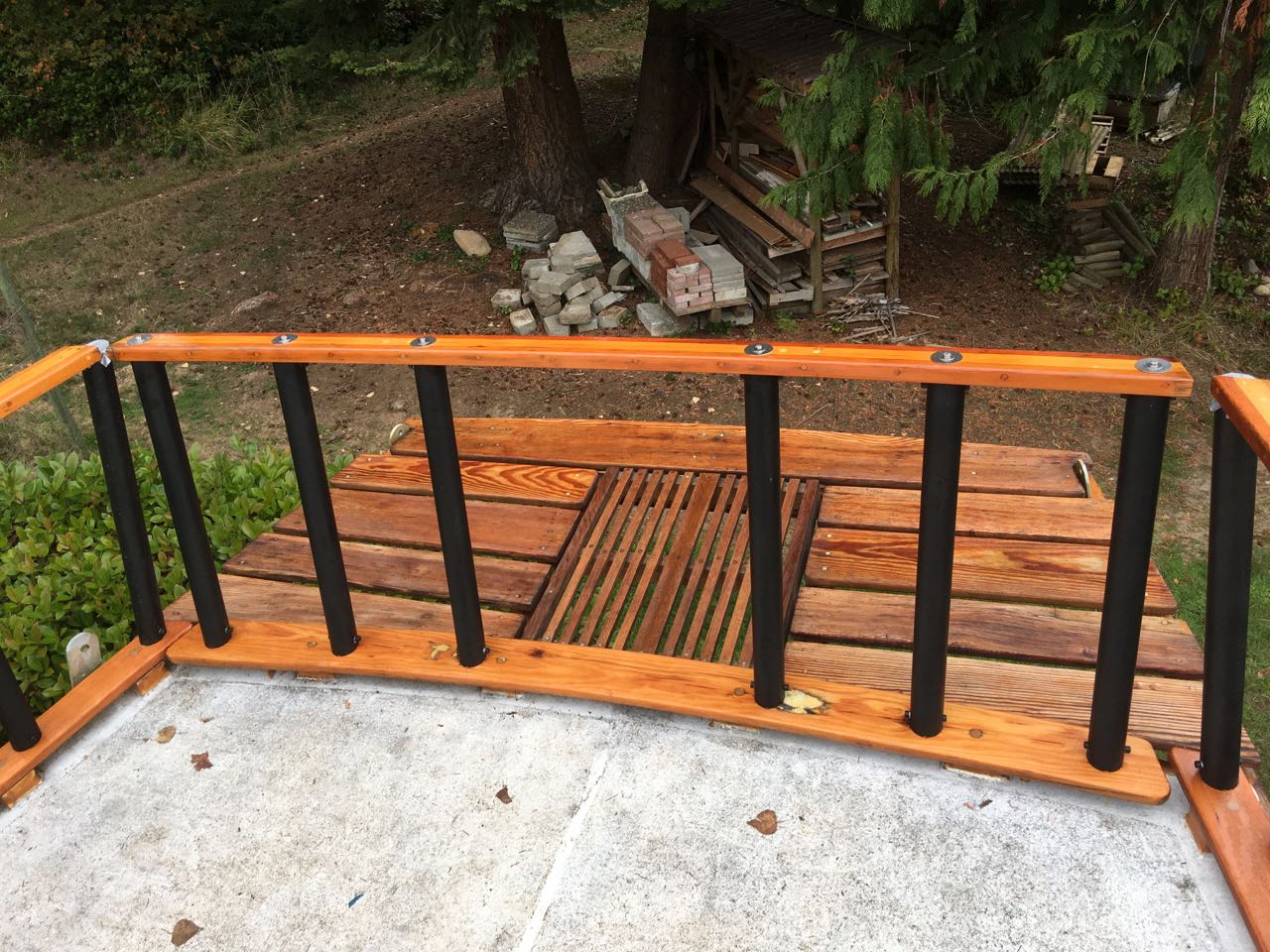 |
|
Handrail fitted. All I need to do is attach the ends together. |
|
|
|